Łączenie dwóch kompresorów to proces, który wymaga staranności oraz zrozumienia zasad działania tych urządzeń. W pierwszej kolejności należy zidentyfikować, jakie kompresory posiadamy oraz jakie mają parametry techniczne. Ważne jest, aby obydwa kompresory miały podobne ciśnienie robocze oraz wydajność, co pozwoli na ich efektywne współdziałanie. Należy również zwrócić uwagę na rodzaj napędu, ponieważ różne systemy mogą wymagać innych rozwiązań. Kolejnym krokiem jest zaplanowanie układu połączeń, które powinny być wykonane z odpowiednich materiałów odpornych na wysokie ciśnienie i korozję. Warto również pomyśleć o zastosowaniu zaworów bezpieczeństwa, które zabezpieczą nas przed ewentualnymi awariami.
Co warto wiedzieć przed połączeniem dwóch kompresorów?
Przed przystąpieniem do łączenia dwóch kompresorów warto zasięgnąć porady specjalistów lub dokładnie zapoznać się z dokumentacją techniczną obu urządzeń. Istotnym aspektem jest również dobór odpowiednich akcesoriów, takich jak rury, złączki czy zawory, które będą musiały sprostać wymaganiom ciśnieniowym. Warto również uwzględnić miejsce instalacji, ponieważ oba kompresory powinny być umiejscowione w sposób umożliwiający łatwy dostęp do nich w razie potrzeby serwisowania. Dobrze jest także rozważyć zastosowanie systemu filtracji powietrza, który poprawi jakość sprężonego powietrza oraz wydłuży żywotność urządzeń. Nie można zapominać o regularnych przeglądach i konserwacji sprzętu, co pozwoli na uniknięcie wielu problemów związanych z jego eksploatacją.
Jakie są zalety łączenia dwóch kompresorów?
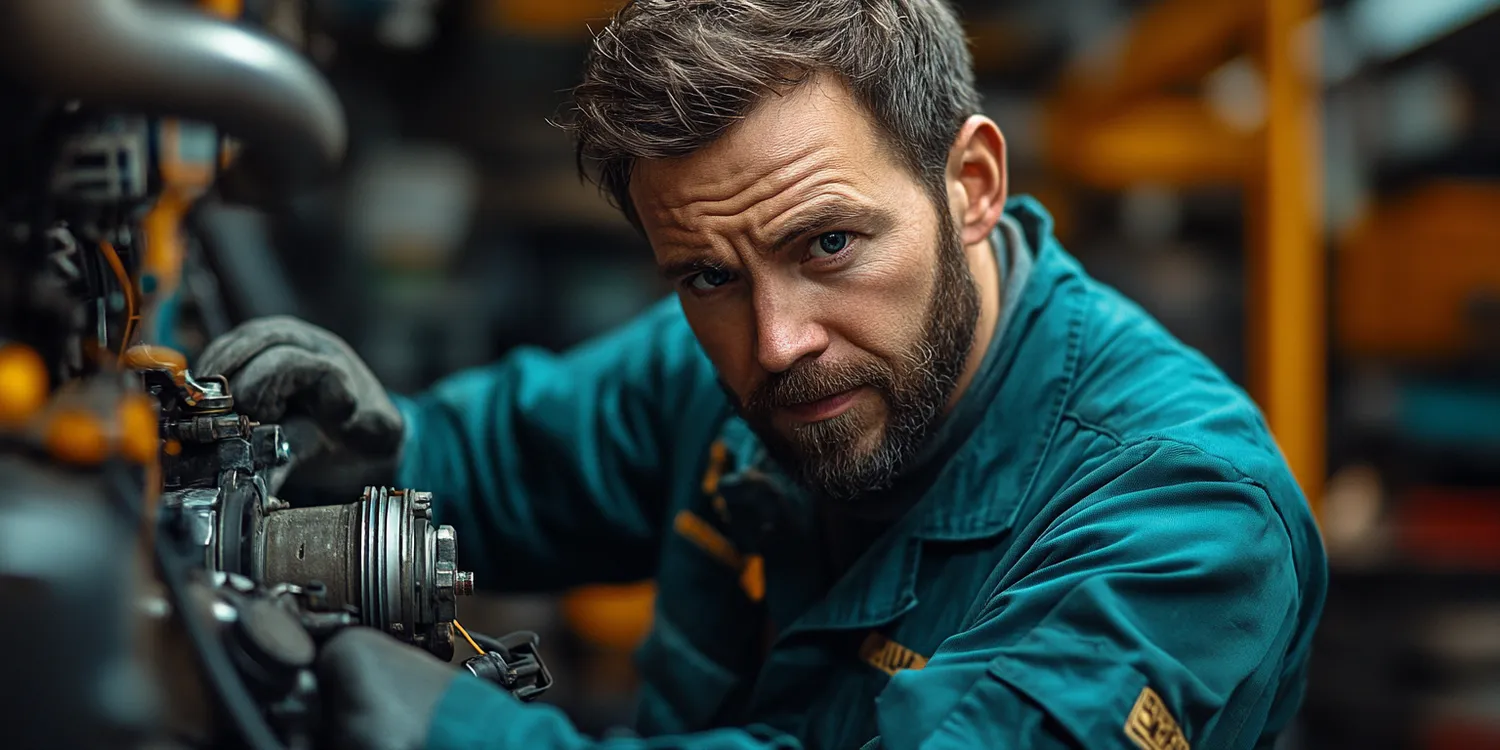
Łączenie dwóch kompresorów niesie ze sobą wiele korzyści, które mogą znacząco wpłynąć na efektywność pracy w różnych branżach. Przede wszystkim zwiększa to wydajność całego systemu sprężonego powietrza, co jest szczególnie istotne w zakładach przemysłowych czy warsztatach. Dzięki połączeniu dwóch jednostek można uzyskać większą ilość sprężonego powietrza przy zachowaniu stabilnego ciśnienia roboczego. To z kolei umożliwia jednoczesne zasilanie kilku narzędzi pneumatycznych lub maszyn, co przyspiesza procesy produkcyjne i zwiększa ich efektywność. Ponadto łączenie kompresorów może prowadzić do oszczędności energetycznych, ponieważ jeden większy system może być bardziej efektywny niż dwa mniejsze działające niezależnie.
Jakie są najczęstsze błędy przy łączeniu kompresorów?
Podczas łączenia dwóch kompresorów można napotkać wiele pułapek i błędów, które mogą prowadzić do poważnych problemów eksploatacyjnych. Jednym z najczęstszych błędów jest niewłaściwe dobranie parametrów technicznych obu urządzeń. Jeśli jeden kompresor ma znacznie wyższą wydajność niż drugi, może to prowadzić do przeciążenia słabszej jednostki oraz jej szybszego zużycia. Innym powszechnym problemem jest niewłaściwe wykonanie połączeń hydraulicznych lub pneumatycznych, co może skutkować wyciekami powietrza i obniżeniem efektywności całego systemu. Zdarza się również ignorowanie zasad bezpieczeństwa – brak zaworów bezpieczeństwa czy niewłaściwe materiały mogą prowadzić do niebezpiecznych sytuacji podczas pracy urządzeń.
Jakie narzędzia będą potrzebne do połączenia kompresorów?
Przy łączeniu dwóch kompresorów kluczowe jest posiadanie odpowiednich narzędzi, które umożliwią wykonanie tego zadania w sposób bezpieczny i efektywny. W pierwszej kolejności warto zaopatrzyć się w podstawowe narzędzia ręczne, takie jak klucze płaskie i nasadowe, które będą niezbędne do montażu złączek oraz rur. Dodatkowo, przydatne będą również szczypce oraz wkrętaki, które ułatwią manipulację przy drobniejszych elementach. Kolejnym istotnym narzędziem jest piła do metalu lub rury, która pozwoli na precyzyjne przycięcie elementów instalacji do odpowiednich wymiarów. Warto również pomyśleć o użyciu narzędzi pomiarowych, takich jak poziomica czy miara, aby upewnić się, że wszystkie elementy są zamontowane w odpowiednich miejscach. Nie można zapominać o sprzęcie ochronnym, takim jak rękawice czy okulary ochronne, które zapewnią bezpieczeństwo podczas pracy.
Jakie są różnice między różnymi typami kompresorów?
Wybór odpowiednich kompresorów do połączenia powinien być uzależniony od ich typu oraz zastosowania. Na rynku dostępne są różne rodzaje kompresorów, takie jak tłokowe, śrubowe czy spiralne, a każdy z nich ma swoje unikalne cechy i zastosowania. Kompresory tłokowe charakteryzują się prostą budową oraz stosunkowo niskimi kosztami zakupu, co czyni je popularnym wyborem w małych warsztatach i gospodarstwach domowych. Z kolei kompresory śrubowe są bardziej wydajne i przeznaczone do pracy ciągłej w przemyśle, gdzie wymagane jest stałe dostarczanie sprężonego powietrza. Kompresory spiralne to nowoczesne rozwiązania, które oferują wysoką efektywność energetyczną oraz niski poziom hałasu. Przy łączeniu różnych typów kompresorów należy zwrócić uwagę na ich parametry techniczne oraz sposób działania, ponieważ niewłaściwe połączenie może prowadzić do problemów z wydajnością oraz trwałością urządzeń.
Jakie są zasady bezpieczeństwa przy łączeniu kompresorów?
Bezpieczeństwo podczas łączenia dwóch kompresorów jest kluczowym aspektem, który należy brać pod uwagę na każdym etapie pracy. Przede wszystkim przed przystąpieniem do jakichkolwiek działań należy wyłączyć zasilanie obu urządzeń oraz upewnić się, że nie ma w nich sprężonego powietrza. Ważne jest także stosowanie odpowiednich materiałów i akcesoriów odpornych na wysokie ciśnienie oraz korozję, co zminimalizuje ryzyko awarii podczas eksploatacji. Podczas montażu należy przestrzegać instrukcji producenta dotyczących połączeń hydraulicznych i pneumatycznych oraz korzystać z narzędzi zgodnych z normami bezpieczeństwa. Dobrze jest również regularnie kontrolować stan techniczny urządzeń oraz przeprowadzać konserwację zgodnie z zaleceniami producenta. Warto także pamiętać o stosowaniu sprzętu ochronnego, takiego jak rękawice czy okulary ochronne, które zabezpieczą nas przed ewentualnymi urazami podczas pracy.
Jakie są koszty związane z połączeniem dwóch kompresorów?
Koszty związane z łączeniem dwóch kompresorów mogą się znacznie różnić w zależności od wielu czynników, takich jak rodzaj użytych urządzeń, materiały potrzebne do montażu oraz ewentualne usługi specjalistyczne. W pierwszej kolejności należy uwzględnić koszt zakupu drugiego kompresora, który będzie musiał być dopasowany do istniejącego systemu. Następnie trzeba doliczyć wydatki na akcesoria montażowe, takie jak rury, złączki czy zawory bezpieczeństwa – ich cena może się różnić w zależności od jakości i producenta. Warto również rozważyć koszty robocizny, jeśli zdecydujemy się na skorzystanie z usług specjalisty lub firmy zajmującej się instalacją systemów pneumatycznych. Dodatkowo nie można zapominać o przyszłych kosztach eksploatacyjnych związanych z utrzymaniem obu urządzeń w dobrym stanie technicznym.
Jakie są najczęstsze pytania dotyczące łączenia kompresorów?
Łączenie dwóch kompresorów budzi wiele pytań zarówno wśród amatorów, jak i profesjonalistów zajmujących się tym tematem. Jednym z najczęściej zadawanych pytań jest to, czy można łączyć różne typy kompresorów – odpowiedź brzmi: tak, ale wymaga to szczególnej uwagi przy doborze parametrów technicznych oraz sposobu połączenia. Innym popularnym zagadnieniem jest kwestia wydajności – wiele osób zastanawia się, czy połączenie dwóch jednostek rzeczywiście zwiększy ilość sprężonego powietrza i jakie będą tego konsekwencje dla całego systemu. Często pojawia się także pytanie o bezpieczeństwo – użytkownicy chcą wiedzieć, jakie środki ostrożności należy podjąć podczas montażu i eksploatacji połączonych kompresorów. Warto również zwrócić uwagę na kwestie związane z konserwacją – wiele osób pyta o to, jak często należy przeprowadzać przeglądy i jakie czynności są niezbędne dla utrzymania sprzętu w dobrym stanie technicznym.
Jakie są najlepsze praktyki przy łączeniu kompresorów?
Aby skutecznie połączyć dwa kompresory i zapewnić ich optymalną pracę, warto zastosować kilka najlepszych praktyk. Po pierwsze kluczowe jest dokładne zaplanowanie całego procesu – przed przystąpieniem do działania warto stworzyć schemat instalacji oraz listę niezbędnych materiałów i narzędzi. Dzięki temu unikniemy niepotrzebnych opóźnień i błędów podczas montażu. Po drugie ważne jest przestrzeganie zasad bezpieczeństwa – zawsze należy wyłączyć zasilanie obu urządzeń przed rozpoczęciem prac oraz korzystać ze sprzętu ochronnego. Kolejną istotną praktyką jest regularna kontrola stanu technicznego zarówno połączonych kompresorów, jak i całego systemu sprężonego powietrza – pozwoli to na szybkie wykrycie ewentualnych usterek i ich naprawę zanim staną się poważnym problemem. Warto również inwestować w szkolenia dla pracowników obsługujących systemy pneumatyczne – dobrze przeszkolony personel będzie miał większą świadomość zagrożeń oraz umiejętność radzenia sobie w sytuacjach awaryjnych.
Jakie są zalety korzystania z dwóch kompresorów jednocześnie?
Korzystanie z dwóch kompresorów jednocześnie może przynieść wiele korzyści, które znacząco poprawiają efektywność i wydajność pracy w różnych zastosowaniach. Po pierwsze, podwójne źródło sprężonego powietrza pozwala na zwiększenie wydajności systemu, co jest szczególnie istotne w zakładach przemysłowych, gdzie wymagane jest stałe zasilanie wielu narzędzi pneumatycznych. Dodatkowo, połączenie dwóch kompresorów może prowadzić do lepszego zarządzania obciążeniem – w przypadku awarii jednego z urządzeń, drugie może nadal pracować, co minimalizuje ryzyko przestojów w produkcji. Kolejną zaletą jest możliwość dostosowania ciśnienia roboczego do różnych potrzeb – można skonfigurować system tak, aby jeden kompresor działał przy wyższym ciśnieniu, a drugi przy niższym, co daje większą elastyczność w zastosowaniach. Warto również zwrócić uwagę na oszczędności energetyczne – dobrze zaprojektowany system z dwoma kompresorami może być bardziej efektywny niż jeden duży kompresor, co przekłada się na niższe koszty eksploatacji.