Destylator przemysłowy to urządzenie służące do separacji cieczy na podstawie różnicy w temperaturze wrzenia. W procesie destylacji, ciecz jest podgrzewana, co powoduje jej parowanie. Para następnie przechodzi przez skraplacz, gdzie schładza się i kondensuje z powrotem do postaci cieczy. Ten proces pozwala na oddzielenie składników o różnych temperaturach wrzenia, co jest kluczowe w wielu branżach, takich jak przemysł chemiczny, petrochemiczny czy farmaceutyczny. W zależności od zastosowania, destylatory mogą być projektowane w różnych rozmiarach i konfiguracjach. W przemyśle często wykorzystuje się destylatory kolumnowe, które charakteryzują się dużą efektywnością separacji dzięki wielokrotnemu skraplaniu i parowaniu. Warto zaznaczyć, że skuteczność destylacji zależy nie tylko od konstrukcji urządzenia, ale także od właściwości chemicznych substancji, które mają być oddzielane.
Jakie są zastosowania destylatorów przemysłowych w różnych branżach
Destylatory przemysłowe znajdują szerokie zastosowanie w wielu branżach, co czyni je niezwykle ważnym elementem procesów produkcyjnych. W przemyśle chemicznym są wykorzystywane do oczyszczania surowców oraz produkcji różnorodnych substancji chemicznych. Na przykład, w produkcji alkoholu etylowego destylacja jest kluczowym etapem, który pozwala na uzyskanie wysokiej czystości trunków. W przemyśle petrochemicznym destylatory służą do separacji frakcji ropy naftowej, co umożliwia uzyskanie paliw oraz innych produktów naftowych. Również w przemyśle farmaceutycznym destylacja odgrywa istotną rolę w produkcji leków i substancji czynnych. Kolejnym przykładem zastosowania destylatorów jest przemysł spożywczy, gdzie wykorzystywane są do ekstrakcji olejków eterycznych z roślin czy produkcji aromatów.
Jakie są różnice między destylatorami a innymi metodami separacji
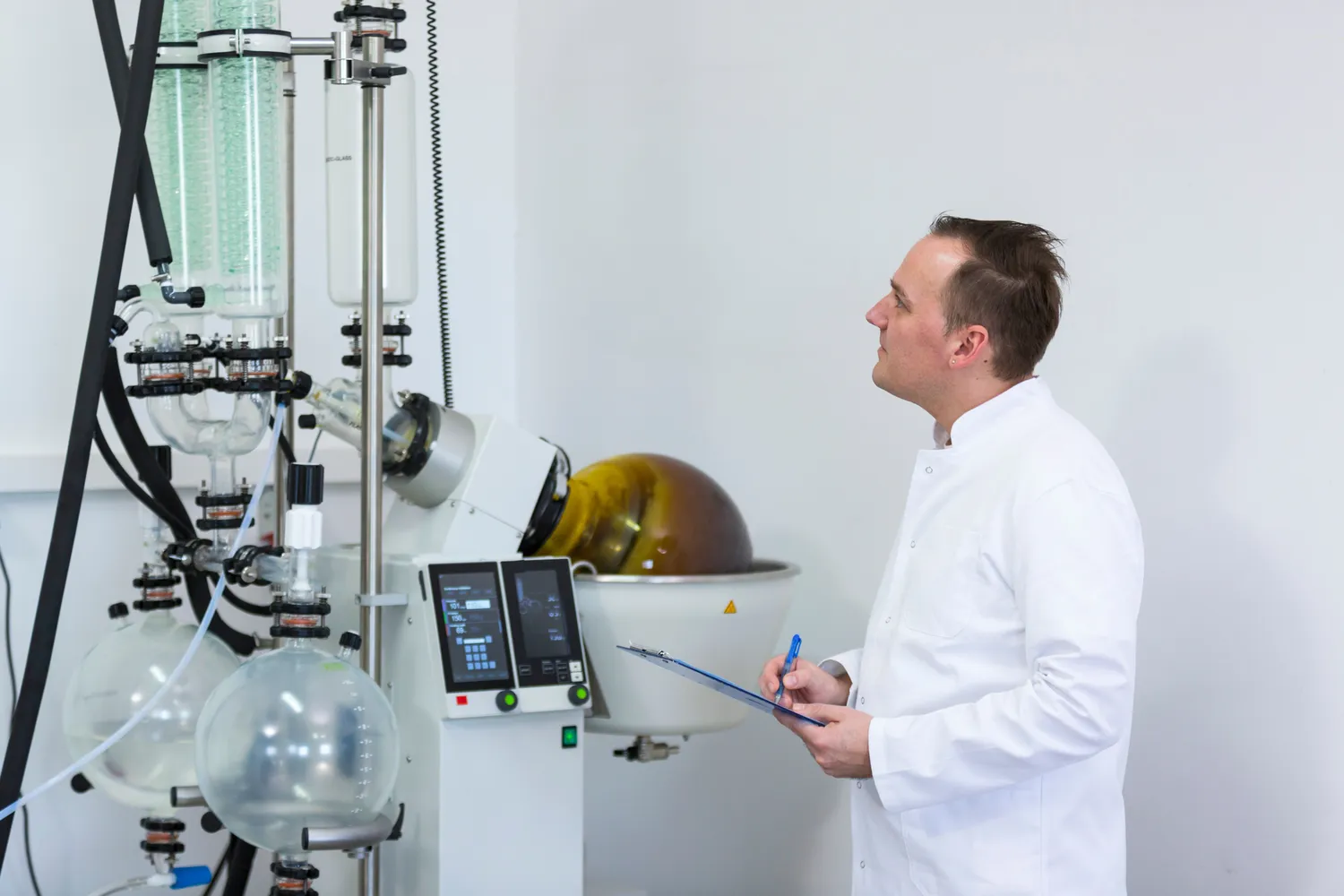
Wybór metody separacji substancji chemicznych ma kluczowe znaczenie dla efektywności procesów przemysłowych. Destylacja różni się od innych metod separacji, takich jak filtracja czy ekstrakcja, głównie ze względu na mechanizm działania oraz zastosowanie. Filtracja polega na oddzieleniu ciał stałych od cieczy za pomocą materiału filtracyjnego, co sprawia, że jest bardziej odpowiednia do oczyszczania zawiesin niż do separacji składników o podobnych właściwościach fizykochemicznych. Ekstrakcja z kolei opiera się na różnicy rozpuszczalności składników w różnych rozpuszczalnikach i może być stosowana do oddzielania substancji organicznych z mieszanin wodnych. Destylacja natomiast jest szczególnie efektywna w przypadku cieczy o różnych temperaturach wrzenia, co czyni ją idealnym rozwiązaniem dla procesów wymagających wysokiej czystości produktów końcowych.
Jakie są najważniejsze aspekty projektowania destylatora przemysłowego
Projektowanie destylatora przemysłowego wymaga uwzględnienia wielu kluczowych aspektów technicznych oraz ekonomicznych. Przede wszystkim należy określić rodzaj substancji, które będą poddawane procesowi destylacji oraz ich właściwości fizykochemiczne, takie jak temperatura wrzenia czy lepkość. Ważnym elementem jest również wybór odpowiedniej konfiguracji urządzenia – może to być destylator prosty lub kolumnowy, w zależności od wymagań dotyczących efektywności separacji oraz skali produkcji. Kolejnym istotnym aspektem jest dobór materiałów konstrukcyjnych, które muszą być odporne na działanie wysokich temperatur oraz agresywnych substancji chemicznych. Należy także uwzględnić kwestie związane z bezpieczeństwem pracy oraz ochroną środowiska, co staje się coraz bardziej istotne w kontekście regulacji prawnych dotyczących emisji zanieczyszczeń.
Jakie są koszty eksploatacji destylatora przemysłowego
Koszty eksploatacji destylatora przemysłowego są kluczowym czynnikiem, który należy wziąć pod uwagę przy planowaniu inwestycji w tego typu urządzenia. Koszty te obejmują zarówno wydatki na energię, jak i konserwację oraz materiały eksploatacyjne. W przypadku destylatorów, które wymagają podgrzewania cieczy, zużycie energii może stanowić znaczną część całkowitych kosztów operacyjnych. Warto zainwestować w nowoczesne technologie, które pozwalają na optymalizację zużycia energii, co z kolei przekłada się na niższe koszty eksploatacji. Ponadto, regularna konserwacja urządzenia jest niezbędna do zapewnienia jego efektywności i długowieczności. Koszty związane z naprawami oraz wymianą części mogą być znaczne, dlatego warto rozważyć umowy serwisowe z dostawcami sprzętu. Dodatkowo, należy uwzględnić koszty związane z kontrolą jakości produktów końcowych oraz ewentualnymi stratami materiałowymi wynikającymi z nieefektywnego procesu destylacji.
Jakie są najnowsze technologie w dziedzinie destylacji przemysłowej
W ostatnich latach nastąpił znaczny postęp technologiczny w dziedzinie destylacji przemysłowej, co przyczyniło się do zwiększenia efektywności i redukcji kosztów operacyjnych. Nowoczesne destylatory często wykorzystują zaawansowane systemy automatyzacji, które umożliwiają precyzyjne kontrolowanie parametrów procesu, takich jak temperatura czy ciśnienie. Dzięki temu możliwe jest osiągnięcie wyższej jakości produktów końcowych oraz zmniejszenie strat materiałowych. Kolejnym innowacyjnym rozwiązaniem są destylatory membranowe, które wykorzystują różnice w przepuszczalności membran do separacji składników. Ta technologia charakteryzuje się mniejszym zużyciem energii oraz możliwością pracy w niższych temperaturach, co jest korzystne dla niektórych delikatnych substancji chemicznych. Warto również zwrócić uwagę na rozwój technologii odzysku ciepła, która pozwala na ponowne wykorzystanie energii generowanej podczas procesu destylacji. Takie podejście nie tylko obniża koszty operacyjne, ale także przyczynia się do zmniejszenia wpływu na środowisko naturalne.
Jakie są najczęstsze problemy związane z użytkowaniem destylatorów przemysłowych
Użytkowanie destylatorów przemysłowych wiąże się z różnymi wyzwaniami i problemami, które mogą wpłynąć na efektywność procesu oraz jakość produktów końcowych. Jednym z najczęstszych problemów jest osadzanie się zanieczyszczeń wewnątrz urządzenia, co może prowadzić do obniżenia wydajności oraz konieczności częstszego czyszczenia. Osady mogą powstawać w wyniku reakcji chemicznych zachodzących podczas destylacji lub z powodu obecności nieczystości w surowcach. Innym istotnym problemem jest kontrola temperatury i ciśnienia, które muszą być ściśle monitorowane, aby zapewnić optymalne warunki pracy urządzenia. W przypadku ich nieprawidłowego ustawienia może dojść do przegrzewania lub niedogrzewania cieczy, co negatywnie wpływa na proces separacji. Również awarie mechaniczne mogą stanowić poważne zagrożenie dla ciągłości produkcji i wymagać kosztownych napraw.
Jakie są różnice między małymi a dużymi destylatorami przemysłowymi
Różnice między małymi a dużymi destylatorami przemysłowymi dotyczą wielu aspektów, w tym konstrukcji, wydajności oraz zastosowań. Małe destylatory często wykorzystywane są w laboratoriach lub małych zakładach produkcyjnych i charakteryzują się prostszą konstrukcją oraz mniejszymi wymaganiami dotyczącymi przestrzeni montażowej. Zazwyczaj mają one ograniczoną wydajność i są przeznaczone do produkcji niewielkich ilości substancji chemicznych lub alkoholu. Duże destylatory przemysłowe natomiast są zaprojektowane do pracy w skali masowej i mogą obsługiwać znacznie większe ilości surowców. Ich konstrukcja jest bardziej skomplikowana, co pozwala na osiągnięcie wyższej efektywności separacji dzięki zastosowaniu kolumn czy systemów wielostopniowych. Różnice te wpływają także na koszty inwestycji oraz eksploatacji – duże destylatory wymagają większych nakładów finansowych zarówno na zakup, jak i utrzymanie.
Jakie są perspektywy rozwoju technologii destylacji przemysłowej
Perspektywy rozwoju technologii destylacji przemysłowej są bardzo obiecujące, zwłaszcza w kontekście rosnących wymagań dotyczących efektywności energetycznej oraz ochrony środowiska. W miarę jak branża przemysłowa staje przed wyzwaniami związanymi ze zmianami klimatycznymi i koniecznością redukcji emisji gazów cieplarnianych, innowacje w dziedzinie destylacji stają się kluczowe dla przyszłości wielu procesów produkcyjnych. Rozwój technologii odzysku ciepła oraz zastosowanie odnawialnych źródeł energii mogą znacząco obniżyć koszty operacyjne oraz wpływ na środowisko naturalne. Ponadto rosnące zainteresowanie biotechnologią otwiera nowe możliwości zastosowania procesów destylacyjnych w produkcji biopaliw czy substancji chemicznych pochodzenia biologicznego. Warto również zauważyć, że rozwój sztucznej inteligencji i automatyzacji może przyczynić się do dalszej optymalizacji procesów destylacyjnych poprzez lepsze monitorowanie i kontrolę parametrów pracy urządzeń.
Jakie są kluczowe czynniki wpływające na efektywność destylacji
Efektywność procesu destylacji przemysłowej zależy od wielu kluczowych czynników, które mają istotny wpływ na jakość i ilość uzyskiwanych produktów. Przede wszystkim, temperatura i ciśnienie są fundamentalnymi parametrami, które muszą być ściśle kontrolowane, aby zapewnić optymalne warunki dla separacji składników. Zbyt wysoka temperatura może prowadzić do niepożądanych reakcji chemicznych, podczas gdy zbyt niskie wartości mogą skutkować niewystarczającą efektywnością procesu. Kolejnym istotnym czynnikiem jest czas kontaktu między parą a cieczą, który powinien być odpowiednio dostosowany do rodzaju substancji poddawanej destylacji. Warto również zwrócić uwagę na jakość surowców, ponieważ obecność zanieczyszczeń może negatywnie wpłynąć na proces oraz jakość końcowego produktu. Dodatkowo, konstrukcja samego destylatora oraz zastosowane materiały mają znaczenie dla efektywności operacji.