Destylacja rozpuszczalników to proces, który polega na oddzieleniu składników mieszaniny na podstawie różnic w ich temperaturach wrzenia. W praktyce oznacza to, że podczas podgrzewania cieczy, składniki o niższej temperaturze wrzenia przechodzą w stan gazowy, a następnie skraplają się w chłodniejszej części aparatury destylacyjnej. Kluczowym elementem tego procesu jest zastosowanie odpowiednich urządzeń, takich jak kolumny destylacyjne czy alembiki, które umożliwiają efektywne oddzielanie substancji. W przypadku destylacji rozpuszczalników istotne jest również zrozumienie właściwości chemicznych i fizycznych substancji, które mają być oddzielane. Na przykład, niektóre rozpuszczalniki mogą tworzyć azeotrop, co utrudnia ich separację. Dlatego ważne jest, aby przed przystąpieniem do destylacji dokładnie zbadać charakterystykę mieszaniny oraz wybrać odpowiednią metodę, która zapewni najlepsze wyniki.
Jakie są rodzaje destylacji stosowane w laboratoriach
W laboratoriach chemicznych można spotkać różne metody destylacji, które są dostosowane do specyficznych potrzeb i właściwości rozpuszczalników. Najpopularniejsze z nich to destylacja prosta, frakcyjna oraz destylacja próżniowa. Destylacja prosta jest najczęściej stosowana do oddzielania składników o znacznie różniących się temperaturach wrzenia. Proces ten jest stosunkowo łatwy do przeprowadzenia i nie wymaga skomplikowanego sprzętu. Z kolei destylacja frakcyjna jest bardziej zaawansowaną techniką, która pozwala na separację substancji o zbliżonych temperaturach wrzenia. W tym przypadku wykorzystuje się kolumny frakcyjne, które zwiększają efektywność procesu poprzez wielokrotne skraplanie i parowanie. Destylacja próżniowa natomiast jest stosowana w sytuacjach, gdy substancje są wrażliwe na wysoką temperaturę lub mają bardzo wysokie temperatury wrzenia. Obniżenie ciśnienia pozwala na przeprowadzenie destylacji w niższych temperaturach, co minimalizuje ryzyko degradacji składników.
Jakie są zastosowania destylacji rozpuszczalników w przemyśle
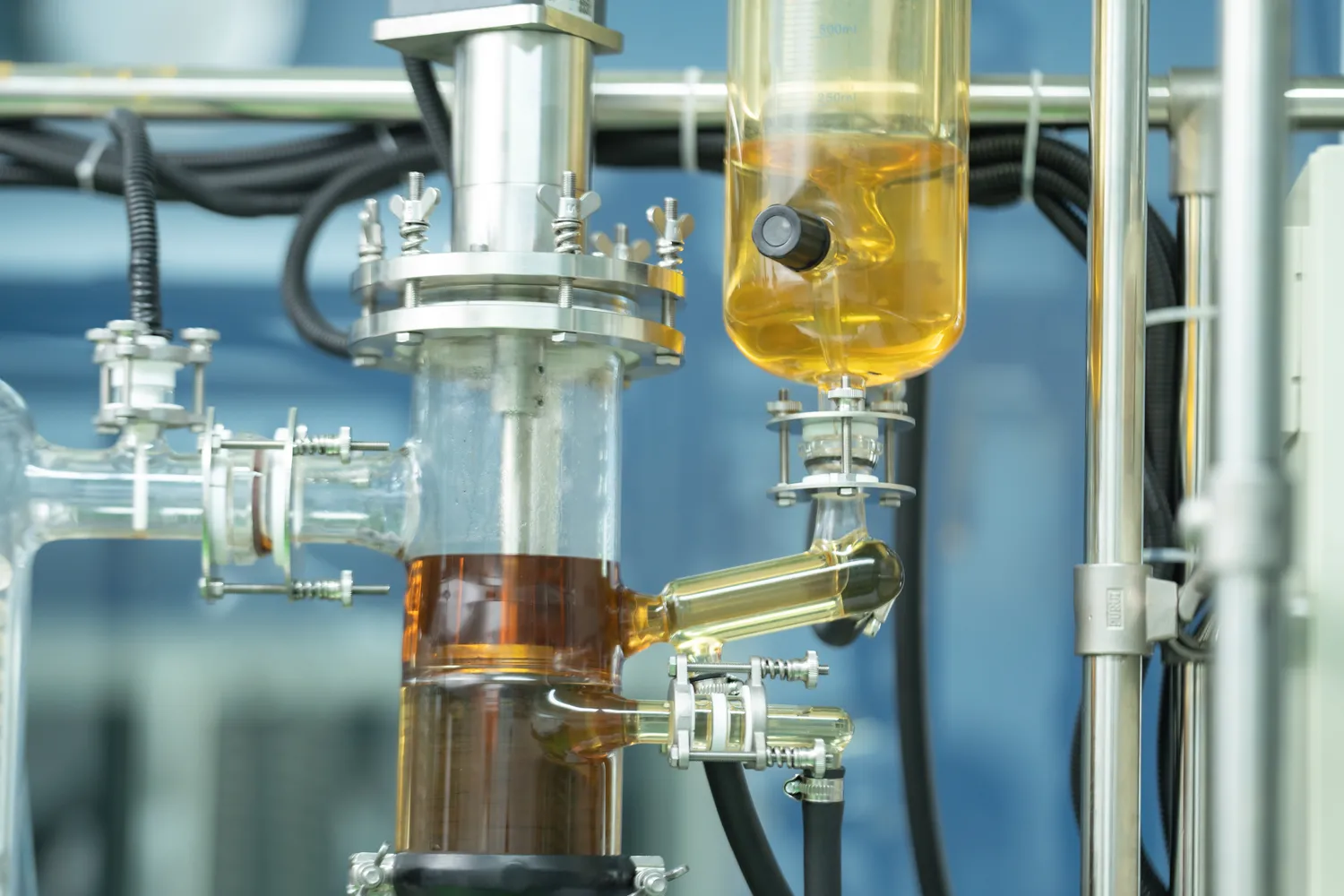
Destylacja rozpuszczalników ma szerokie zastosowanie w różnych gałęziach przemysłu chemicznego oraz farmaceutycznego. W przemyśle chemicznym proces ten jest kluczowy dla produkcji czystych substancji chemicznych oraz ich pochodnych. Na przykład, wiele rozpuszczalników organicznych, takich jak etanol czy aceton, uzyskuje się właśnie poprzez destylację surowców naturalnych lub syntetycznych. W branży farmaceutycznej destylacja odgrywa istotną rolę w oczyszczaniu aktywnych składników leków oraz usuwaniu niepożądanych zanieczyszczeń. Dzięki temu możliwe jest uzyskanie wysokiej jakości produktów farmaceutycznych spełniających rygorystyczne normy bezpieczeństwa i skuteczności. Ponadto destylacja jest także wykorzystywana w produkcji alkoholi spożywczych oraz olejków eterycznych, gdzie kluczowe znaczenie ma zachowanie odpowiednich aromatów i smaków. W kontekście ochrony środowiska proces ten może być stosowany do odzyskiwania rozpuszczalników z odpadów przemysłowych, co przyczynia się do zmniejszenia ilości odpadów oraz oszczędności surowców naturalnych.
Jakie są najczęstsze błędy podczas destylacji rozpuszczalników
Podczas przeprowadzania procesu destylacji rozpuszczalników można napotkać szereg typowych błędów, które mogą wpłynąć na jakość uzyskanego produktu oraz efektywność całego procesu. Jednym z najczęstszych błędów jest niewłaściwe ustawienie temperatury grzania. Zbyt wysoka temperatura może prowadzić do niepożądanej degradacji składników lub ich niepełnej separacji, podczas gdy zbyt niska temperatura może spowodować wydłużenie czasu procesu i obniżenie wydajności. Kolejnym problemem może być niewłaściwe dobranie sprzętu do konkretnej aplikacji; na przykład użycie kolumny frakcyjnej o niewłaściwej wysokości może skutkować niedostatecznym oddzieleniem składników o podobnych temperaturach wrzenia. Ważnym aspektem jest również kontrola ciśnienia; w przypadku destylacji próżniowej niewłaściwe ustawienie ciśnienia może prowadzić do nieefektywnej separacji substancji. Dodatkowo należy zwrócić uwagę na czystość używanych materiałów oraz sprzętu; zanieczyszczenia mogą wpływać na wyniki analizy i jakość końcowego produktu.
Jakie są kluczowe czynniki wpływające na efektywność destylacji rozpuszczalników
Efektywność destylacji rozpuszczalników jest uzależniona od wielu czynników, które mogą znacząco wpłynąć na wyniki procesu. Jednym z najważniejszych aspektów jest temperatura wrzenia poszczególnych składników mieszaniny. Różnice w temperaturach wrzenia pozwalają na ich oddzielenie, dlatego im większa różnica, tym łatwiejszy i bardziej efektywny będzie proces destylacji. Kolejnym kluczowym czynnikiem jest ciśnienie atmosferyczne, które może być regulowane w przypadku destylacji próżniowej. Obniżenie ciśnienia pozwala na przeprowadzenie destylacji w niższych temperaturach, co jest szczególnie istotne dla substancji wrażliwych na ciepło. Oprócz tego, konstrukcja aparatury destylacyjnej ma ogromne znaczenie; kolumny frakcyjne o odpowiedniej wysokości i średnicy mogą znacznie zwiększyć efektywność separacji. Warto również zwrócić uwagę na czas trwania procesu oraz szybkość podgrzewania, ponieważ zbyt szybkie podgrzewanie może prowadzić do niepełnej separacji składników. Wreszcie, jakość używanych materiałów oraz czystość sprzętu mają kluczowe znaczenie dla uzyskania wysokiej jakości produktu końcowego.
Jakie są różnice między destylacją a innymi metodami separacji
Destylacja rozpuszczalników to jedna z wielu metod separacji substancji chemicznych, ale wyróżnia się ona kilkoma istotnymi cechami w porównaniu do innych technik. Na przykład, w przeciwieństwie do ekstrakcji, która polega na rozpuszczaniu składników w odpowiednich rozpuszczalnikach, destylacja wykorzystuje różnice w temperaturach wrzenia do oddzielania substancji. To sprawia, że jest to metoda bardziej odpowiednia dla substancji lotnych. Inną popularną metodą separacji jest filtracja, która polega na oddzielaniu cząstek stałych od cieczy lub gazu za pomocą materiałów filtracyjnych. Filtracja nie jest jednak skuteczna w przypadku mieszanin cieczy, gdzie konieczne jest zastosowanie technik takich jak destylacja. Ponadto istnieje także chromatografia, która umożliwia separację składników na podstawie ich interakcji z fazą stacjonarną i ruchomą. Choć chromatografia może być bardziej precyzyjna i skuteczna w niektórych przypadkach, to jednak wymaga bardziej skomplikowanego sprzętu i dłuższego czasu analizy.
Jakie są najczęstsze zastosowania destylacji w laboratoriach chemicznych
Destylacja rozpuszczalników znajduje szerokie zastosowanie w laboratoriach chemicznych, gdzie służy do różnych celów analitycznych oraz preparatywnych. Jednym z najczęstszych zastosowań jest oczyszczanie substancji chemicznych poprzez usuwanie zanieczyszczeń oraz niepożądanych składników. Dzięki temu można uzyskać wysokiej jakości reagenty potrzebne do dalszych badań czy syntez chemicznych. Destylacja jest również wykorzystywana do przygotowywania standardów odniesienia, które są niezbędne w analizach chemicznych oraz kontrolach jakości produktów. Kolejnym ważnym zastosowaniem jest analiza składu chemicznego próbek; poprzez destylację można oddzielić poszczególne składniki mieszaniny i zbadać ich właściwości fizykochemiczne. W laboratoriach farmaceutycznych proces ten odgrywa kluczową rolę w produkcji leków oraz ich formułowaniu; wiele substancji czynnych uzyskuje się właśnie dzięki destylacji. Dodatkowo destylacja może być stosowana do odzyskiwania rozpuszczalników z odpadów laboratoryjnych, co przyczynia się do ochrony środowiska i oszczędności surowców naturalnych.
Jakie są nowoczesne technologie stosowane w destylacji rozpuszczalników
W ostatnich latach rozwój technologii przyczynił się do znacznych postępów w dziedzinie destylacji rozpuszczalników. Nowoczesne urządzenia i metody pozwalają na zwiększenie efektywności procesu oraz poprawę jakości uzyskiwanych produktów. Przykładem innowacyjnej technologii jest zastosowanie membran do separacji składników mieszaniny; membrany te mogą selektywnie przepuszczać określone substancje, co pozwala na ich oddzielenie bez konieczności podgrzewania całej mieszaniny. Innym przykładem są systemy automatyzacji procesów destylacyjnych, które umożliwiają precyzyjne kontrolowanie parametrów takich jak temperatura czy ciśnienie, co przekłada się na lepsze wyniki i mniejsze ryzyko błędów ludzkich. Warto również wspomnieć o zastosowaniu technologii mikrofalowej w procesach destylacyjnych; mikrofalowe podgrzewanie może przyspieszyć proces separacji i zwiększyć wydajność energetyczną całego systemu. Dodatkowo rozwijają się także metody wykorzystujące nanotechnologię do poprawy efektywności separacji składników poprzez modyfikację powierzchni materiałów używanych w aparaturze destylacyjnej.
Jakie są aspekty bezpieczeństwa podczas przeprowadzania destylacji
Bezpieczeństwo podczas przeprowadzania destylacji rozpuszczalników jest niezwykle istotnym zagadnieniem, które należy uwzględnić na każdym etapie procesu. Przede wszystkim należy pamiętać o właściwej wentylacji pomieszczenia laboratoryjnego; wiele rozpuszczalników jest łatwopalnych lub toksycznych, dlatego zapewnienie odpowiedniej cyrkulacji powietrza może zminimalizować ryzyko pożaru lub zatrucia. Używanie odpowiednich środków ochrony osobistej, takich jak rękawice ochronne, gogle czy fartuchy laboratoryjne, jest również kluczowe dla ochrony zdrowia osób pracujących z niebezpiecznymi substancjami. Ważne jest także regularne sprawdzanie stanu technicznego aparatury destylacyjnej; wszelkie uszkodzenia czy nieszczelności mogą prowadzić do wycieków szkodliwych oparów lub cieczy. Należy również przestrzegać zasad dotyczących przechowywania i transportu rozpuszczalników; stosowanie odpowiednich pojemników oraz oznakowanie substancji to podstawowe zasady bezpieczeństwa.
Jakie są przyszłe kierunki badań nad destylacją rozpuszczalników
Przyszłość badań nad destylacją rozpuszczalników zapowiada się obiecująco dzięki ciągłemu rozwojowi technologii oraz rosnącemu zainteresowaniu zrównoważonymi metodami produkcji chemicznej. Wśród kluczowych kierunków badań można wymienić rozwój nowych materiałów dla kolumn frakcyjnych oraz membran separacyjnych, które mogą zwiększyć efektywność procesu oraz obniżyć koszty operacyjne. Badania nad zastosowaniem nanotechnologii mogą prowadzić do stworzenia innowacyjnych systemów separacyjnych o wyższej wydajności i mniejszym zużyciu energii. Ponadto rośnie zainteresowanie metodami ekologicznymi, takimi jak wykorzystanie bioprocese czy zielonych rozpuszczalników, co może przyczynić się do zmniejszenia negatywnego wpływu przemysłu chemicznego na środowisko naturalne.