Budowa maszyn pneumatycznych opiera się na kilku kluczowych elementach, które współpracują ze sobą, aby zapewnić efektywne działanie systemu. Na początku warto zwrócić uwagę na kompresor, który jest sercem całego układu. Jego zadaniem jest sprężanie powietrza, co pozwala na uzyskanie odpowiedniego ciśnienia niezbędnego do pracy maszyny. Kolejnym istotnym elementem jest zbiornik powietrza, który gromadzi sprężone powietrze i zapewnia jego stabilny przepływ do pozostałych części układu. W maszynach pneumatycznych niezbędne są także zawory, które kontrolują kierunek i przepływ powietrza w systemie. Zawory te mogą być ręczne lub automatyczne, a ich wybór zależy od specyfiki zastosowania. Ponadto, w budowie maszyn pneumatycznych kluczową rolę odgrywają siłowniki pneumatyczne, które przekształcają energię sprężonego powietrza na ruch mechaniczny. Siłowniki te mogą mieć różne kształty i rozmiary, co pozwala na ich dostosowanie do konkretnych potrzeb aplikacji. Ostatnim, ale nie mniej ważnym elementem są przewody pneumatyczne, które łączą wszystkie komponenty systemu i umożliwiają transport sprężonego powietrza.
Jakie są zalety i wady maszyn pneumatycznych
Maszyny pneumatyczne mają wiele zalet, które sprawiają, że są popularnym wyborem w różnych branżach przemysłowych. Przede wszystkim charakteryzują się dużą prostotą konstrukcji oraz łatwością w obsłudze. Dzięki temu można je szybko uruchomić oraz zintegrować z innymi systemami produkcyjnymi. Ponadto maszyny pneumatyczne są stosunkowo lekkie w porównaniu do ich elektrycznych odpowiedników, co ułatwia ich transport oraz instalację. Dodatkowo sprężone powietrze jako medium robocze jest powszechnie dostępne i tanie, co przekłada się na niższe koszty eksploatacji. Niemniej jednak istnieją również pewne wady związane z używaniem maszyn pneumatycznych. Jedną z nich jest konieczność posiadania odpowiednich urządzeń do sprężania powietrza, co wiąże się z dodatkowymi kosztami inwestycyjnymi. Ponadto w przypadku awarii kompresora cały system może przestać działać, co prowadzi do przestojów w produkcji. Innym problemem jest ograniczona precyzja działania siłowników pneumatycznych w porównaniu do siłowników elektrycznych, co może być istotne w aplikacjach wymagających dużej dokładności.
Jakie zastosowania mają maszyny pneumatyczne w przemyśle
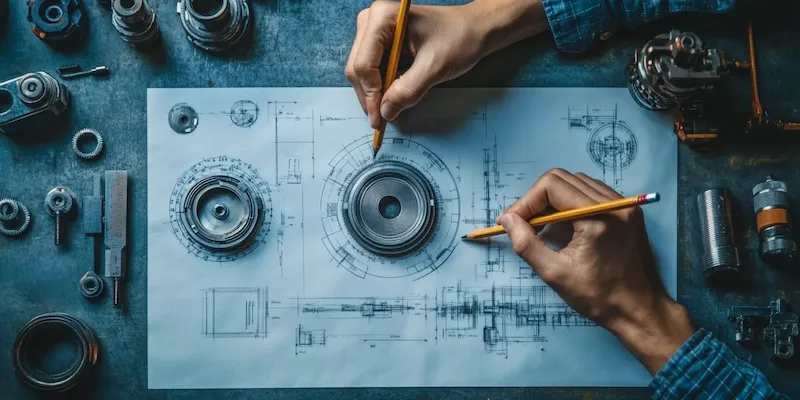
Maszyny pneumatyczne znajdują szerokie zastosowanie w różnych dziedzinach przemysłu ze względu na swoją wszechstronność oraz efektywność działania. W przemyśle produkcyjnym często wykorzystuje się je do automatyzacji procesów montażowych oraz pakowania produktów. Siłowniki pneumatyczne są idealne do wykonywania ruchów liniowych oraz obrotowych, co sprawia, że doskonale nadają się do obsługi robotów przemysłowych czy linii montażowych. W branży motoryzacyjnej maszyny pneumatyczne są wykorzystywane do malowania pojazdów oraz aplikacji klejów i uszczelniaczy. Dzięki swojej precyzyjnej kontroli nad przepływem powietrza można uzyskać równomierne pokrycie powierzchni bez zacieków czy niedoskonałości. W przemyśle spożywczym maszyny pneumatyczne służą do transportu surowców oraz pakowania gotowych produktów, co przyczynia się do zwiększenia wydajności procesów produkcyjnych. Również w branży farmaceutycznej wykorzystuje się je do napełniania pojemników oraz etykietowania leków. Warto dodać, że maszyny pneumatyczne znajdują zastosowanie także w budownictwie, gdzie używane są do podnoszenia ciężkich materiałów oraz narzędzi budowlanych.
Jakie nowoczesne technologie wpływają na rozwój maszyn pneumatycznych
W ostatnich latach rozwój technologii znacząco wpłynął na budowę maszyn pneumatycznych oraz ich zastosowanie w różnych branżach przemysłowych. Jednym z najważniejszych trendów jest automatyzacja procesów produkcyjnych, która wymaga coraz bardziej zaawansowanych rozwiązań technologicznych. Wprowadzenie inteligentnych systemów sterowania pozwala na precyzyjne zarządzanie pracą maszyn pneumatycznych oraz ich integrację z innymi urządzeniami w zakładzie produkcyjnym. Dzięki zastosowaniu czujników i systemów monitorujących możliwe jest bieżące śledzenie parametrów pracy maszyn oraz szybsze reagowanie na ewentualne awarie czy nieprawidłowości. Kolejnym istotnym aspektem jest rozwój materiałów wykorzystywanych do produkcji elementów maszyn pneumatycznych. Nowoczesne tworzywa sztuczne oraz kompozyty charakteryzują się wysoką odpornością na działanie agresywnych substancji chemicznych oraz ekstremalnych temperatur, co zwiększa trwałość i niezawodność urządzeń. Również technologia druku 3D znajduje zastosowanie w budowie maszyn pneumatycznych, umożliwiając szybkie prototypowanie oraz produkcję skomplikowanych komponentów o niskiej wadze i wysokiej wytrzymałości.
Jakie są kluczowe zasady bezpieczeństwa przy pracy z maszynami pneumatycznymi
Bezpieczeństwo w pracy z maszynami pneumatycznymi jest niezwykle istotne, ponieważ niewłaściwe użytkowanie tych urządzeń może prowadzić do poważnych wypadków. Przede wszystkim, przed rozpoczęciem pracy należy dokładnie zapoznać się z instrukcją obsługi maszyny oraz przeprowadzić odpowiednie szkolenie dla pracowników. Kluczowym elementem jest także regularne przeprowadzanie przeglądów technicznych oraz konserwacji urządzeń, co pozwala na wykrycie ewentualnych usterek i ich naprawę przed wystąpieniem awarii. Warto również zwrócić uwagę na odpowiednie oznakowanie strefy pracy maszyn pneumatycznych, aby zminimalizować ryzyko przypadkowego wejścia osób nieuprawnionych w obszar działania urządzeń. Używanie odpowiednich środków ochrony osobistej, takich jak kaski, gogle czy rękawice, jest niezbędne do zapewnienia bezpieczeństwa pracowników. Należy także pamiętać o właściwym zabezpieczeniu przewodów pneumatycznych, aby uniknąć ich uszkodzenia oraz wycieków sprężonego powietrza, które mogą prowadzić do niebezpiecznych sytuacji. W przypadku awarii lub nieprawidłowego działania maszyny, konieczne jest natychmiastowe jej wyłączenie oraz zgłoszenie problemu do odpowiednich służb technicznych.
Jakie są różnice między maszynami pneumatycznymi a elektrycznymi
Maszyny pneumatyczne i elektryczne różnią się pod wieloma względami, co wpływa na ich zastosowanie w różnych branżach przemysłowych. Przede wszystkim, podstawową różnicą jest źródło energii – maszyny pneumatyczne wykorzystują sprężone powietrze jako medium robocze, podczas gdy maszyny elektryczne działają na zasadzie energii elektrycznej. To sprawia, że maszyny pneumatyczne są często lżejsze i bardziej mobilne, co ułatwia ich transport i instalację w różnych miejscach. Z drugiej strony, maszyny elektryczne zazwyczaj oferują większą precyzję i kontrolę nad procesem produkcyjnym, co czyni je bardziej odpowiednimi do zastosowań wymagających dużej dokładności. Kolejną istotną różnicą jest koszt eksploatacji – sprężone powietrze może być tańsze niż energia elektryczna w dłuższej perspektywie czasowej, jednak koszty związane z zakupem kompresorów oraz ich konserwacją mogą wpłynąć na całkowity bilans finansowy. Warto również zauważyć, że maszyny pneumatyczne są bardziej odporne na działanie czynników zewnętrznych, takich jak wilgoć czy pył, co czyni je idealnym wyborem w trudnych warunkach przemysłowych. Z kolei maszyny elektryczne mogą być bardziej skomplikowane w budowie i wymagają regularnej konserwacji układów elektrycznych.
Jakie innowacje technologiczne zmieniają przyszłość maszyn pneumatycznych
W ostatnich latach obserwujemy dynamiczny rozwój innowacji technologicznych wpływających na budowę i funkcjonowanie maszyn pneumatycznych. Jednym z najważniejszych kierunków rozwoju jest automatyzacja procesów produkcyjnych poprzez integrację systemów pneumatycznych z nowoczesnymi rozwiązaniami informatycznymi. Dzięki zastosowaniu sztucznej inteligencji oraz analizy danych możliwe jest optymalizowanie pracy maszyn oraz przewidywanie potencjalnych awarii jeszcze przed ich wystąpieniem. Kolejnym istotnym trendem jest rozwój technologii Internetu Rzeczy (IoT), która umożliwia zdalne monitorowanie parametrów pracy maszyn pneumatycznych oraz ich integrację z systemami zarządzania produkcją. Dzięki temu przedsiębiorstwa mogą lepiej kontrolować procesy produkcyjne oraz szybko reagować na zmieniające się warunki rynkowe. Innowacyjne rozwiązania obejmują także rozwój materiałów wykorzystywanych do budowy komponentów maszyn pneumatycznych – nowoczesne tworzywa sztuczne oraz kompozyty charakteryzują się wyższą odpornością na uszkodzenia mechaniczne i chemiczne, co zwiększa trwałość urządzeń. Ponadto coraz częściej stosuje się technologie odzyskiwania energii w systemach pneumatycznych, co pozwala na zwiększenie efektywności energetycznej i zmniejszenie kosztów eksploatacyjnych.
Jakie są najczęstsze problemy związane z eksploatacją maszyn pneumatycznych
Eksploatacja maszyn pneumatycznych wiąże się z pewnymi wyzwaniami i problemami, które mogą wpływać na efektywność ich działania. Jednym z najczęstszych problemów jest niewłaściwe ciśnienie sprężonego powietrza w systemie, które może prowadzić do obniżenia wydajności siłowników oraz innych komponentów maszyny. Zbyt niskie ciśnienie skutkuje wolniejszym działaniem urządzeń, natomiast zbyt wysokie może prowadzić do uszkodzenia elementów układu. Innym powszechnym problemem są wycieki powietrza w przewodach lub zaworach, co nie tylko obniża efektywność systemu, ale także zwiększa koszty eksploatacji związane z koniecznością dostarczania dodatkowego sprężonego powietrza. Regularne inspekcje i konserwacja układów pneumatycznych są kluczowe dla minimalizacji tych problemów. Dodatkowo użytkownicy często borykają się z brakiem odpowiedniej wiedzy dotyczącej obsługi maszyn pneumatycznych, co może prowadzić do błędów w ich eksploatacji oraz zwiększonego ryzyka awarii. Ważne jest więc przeprowadzanie szkoleń dla pracowników oraz dostarczanie im niezbędnych informacji o zasadach działania urządzeń.
Jakie są przyszłe trendy w rozwoju maszyn pneumatycznych
Przyszłość maszyn pneumatycznych zapowiada się interesująco dzięki ciągłemu rozwojowi technologii oraz rosnącym wymaganiom rynku przemysłowego. Jednym z głównych trendów będzie dalsza automatyzacja procesów produkcyjnych poprzez integrację systemów pneumatycznych z robotyką i sztuczną inteligencją. Dzięki temu możliwe będzie osiągnięcie jeszcze wyższej wydajności oraz precyzji działania maszyn. Również rozwój technologii Internetu Rzeczy (IoT) wpłynie na sposób monitorowania i zarządzania pracą urządzeń pneumatycznych – dzięki możliwości zbierania danych w czasie rzeczywistym przedsiębiorstwa będą mogły lepiej analizować procesy produkcyjne i podejmować bardziej świadome decyzje dotyczące optymalizacji działań. Ponadto coraz większą uwagę przykłada się do efektywności energetycznej systemów pneumatycznych – innowacyjne rozwiązania mają na celu minimalizację strat energii oraz wykorzystanie odnawialnych źródeł energii do napędu kompresorów i innych urządzeń. Warto także zwrócić uwagę na rozwój materiałów wykorzystywanych do budowy komponentów maszyn – nowe tworzywa sztuczne i kompozyty będą charakteryzować się większą odpornością na działanie agresywnych substancji chemicznych oraz ekstremalnych warunków atmosferycznych.